Building name-The Concordia
Location and site-Washington, D.C. The specific address cannot be used
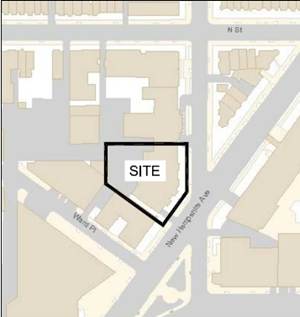
Architecture
Architecture (Design and functional components)-The Concordia is a 10-story plus cellar and underground parking garage extended stay facility with two main structures connected at the ground floor. While the entire building is composed of 178 rooms the bond building has 78 while the Concordia houses the other 100. It was designed in by Berla & Able.
Major national model codes (IBC 2003, BOCA 1999)
IBC 2006/DCMR 12A-2008
IBC 2006/DCMR 12E-2008
IPC 2006/DCMR12F-2008
NFPA NEC 2005/DCMR 12C-2008
IFC 2006/DCMR 12H-2008
IFGC 2006/12I-2008
IEBC 2006/DCMR 12J-2008
ANSI 117.1-2003/DCMR 12A Chapter 11
DCMR Title 11-zoning regulations
District of Columbia Environmental Policy Act of 1989
Green Building Act of 2006
Zoning
DC/R-5-E Overlay (http://maps.dcoz.dc.gov/#)
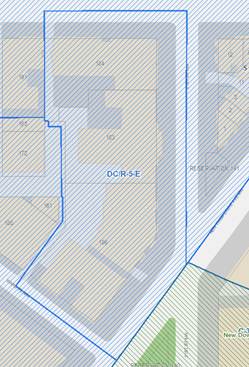
Historical requirements of building or historical district where built.
In 1965 the IMF Concordia was designed by Berla & Able. The building is neither in a historical district nor are there historical requirements for salvaging portions of the building or the building’s façade.
Building enclosure
Building facadesExterior wall type # 12 consists of 6” Batt insulation, 5/8” thick exterior sheathing, liquid applied air barrier, 2” rigid insulation, aluminum clip, sealant with backer rod and shims where required. The last layer to make up the wall is the aluminum composite material panel.
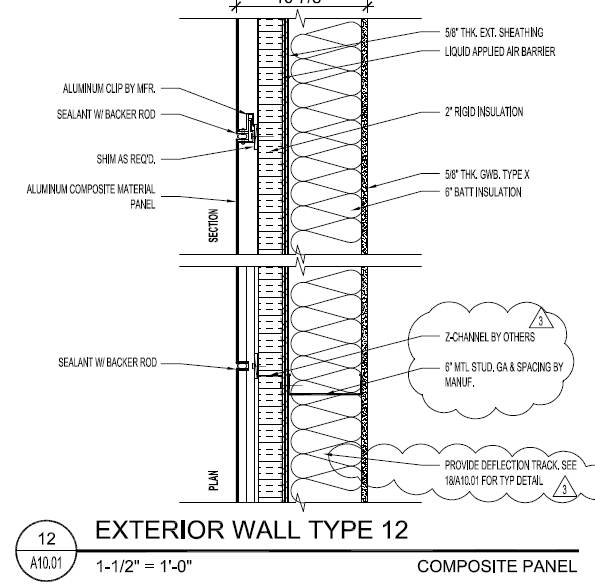
Exterior wall type # 14 will be composed of 7-5/8” thick Concrete Masonry Units (CMU) with a liquid applied air barrier, Z-channel fasteners @ 16” O.C., 2” moisture resistant rigid insulation, required shim to separate aluminum channel from Z-channel, max shims ¾” thick, weeped calcium silicate channel, and finally a calcium silicate masonry unit.
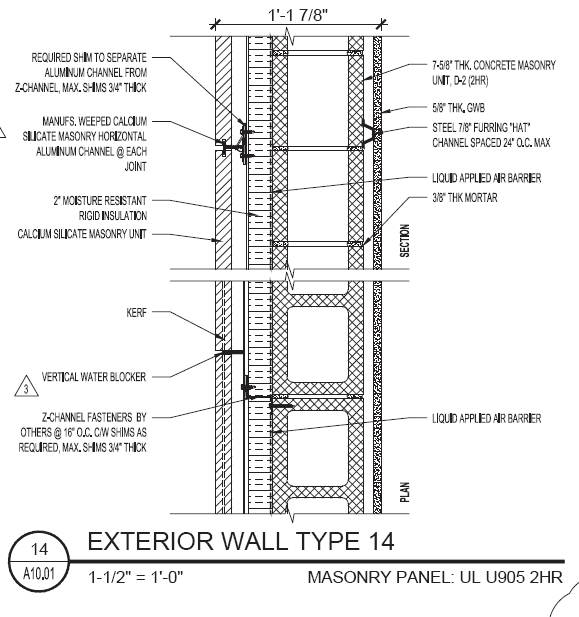
Exterior wall type # 15 has 7-5/8” thick CMUs while wall type 15a has 11-5/8” thick CMUs. They have essentially matching components which include liquid applied air barriers, 2” rigid insulation, aluminum clip, sealant with backer rod and shims where required. The last layer to make up the wall is the aluminum composite material panel.
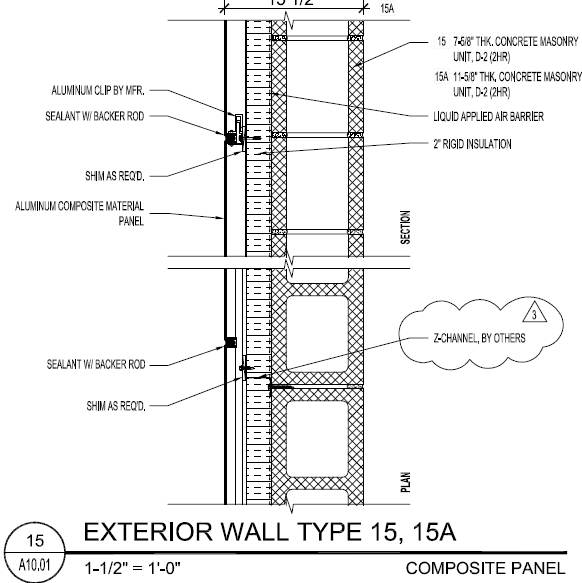
Exterior wall type # 16 has 5-5/8” CMUs, liquid applied air barrier, 2” rigid insulation, 3-5/8” CMU, and lastly metal anchors.
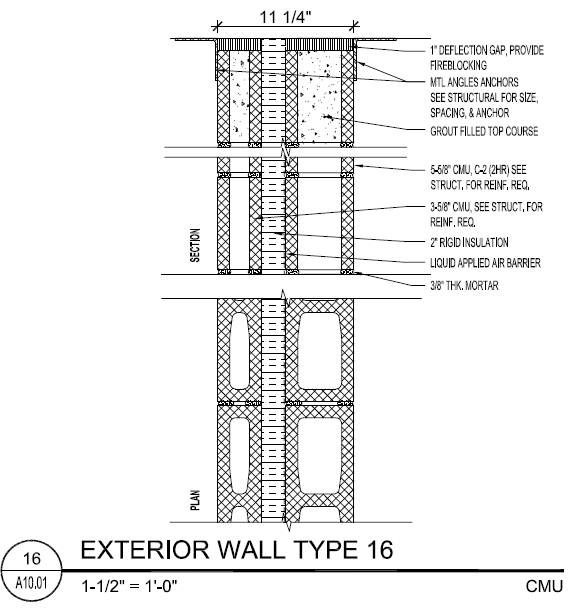
The building façade has an Aluminum Trellis’ and aluminum panels with aluminum coping.
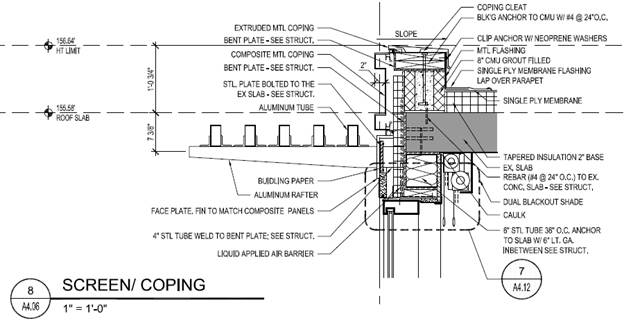
Roofing
The roof is composed of tapered insulation with a 2” base and a single ply membrane both of which rest on the existing slab.
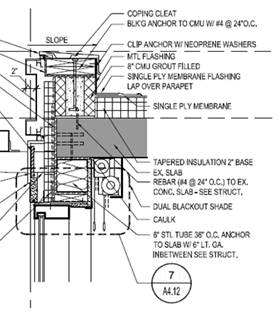
The live planter roofing will consist of a liquid applied air barrier installed on top of the existing slab which will be followed by much thicker tapered insulation, a single ply membrane and lastly live roof planter beds.
Sustainability features
Due to the outdated inefficient systems which were installed when the building was completed this renovation will gut and renovate all the major MEP systems. The renovation of the IMF Concordia is planning to achieve a LEED Gold certification. The goal of achieving this certification will be dependent on the many systems of the structure coming together to produce an efficient building.
Plumbing
The renovation of The Concordia’s will include the installation of Domestic Booster Pumps in order to help produce a more efficient, energy saving plumbing system.
Electrical
Turner’s renovation of the Concordia will include the installation of LED down lights in many of the corridors as well as many other LED fixtures throughout the building.
Mechanical
This renovation will make the building’s mechanical system more efficient by installing 100% outside air packaged energy recovery air handling units and 100% outside air makeup air units
The mechanical system will be improved drastically by installing Variable Refrigerant Volume (VRV) systems. (http://www.mechanicalservicesfiji.com/vrv_aircon.html)
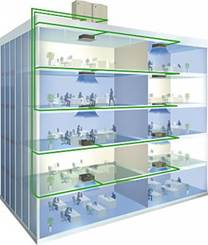
Roofing
The bay roof will have live roof planter beds in order to help reduce the heat island effect as well as storm water runoff.
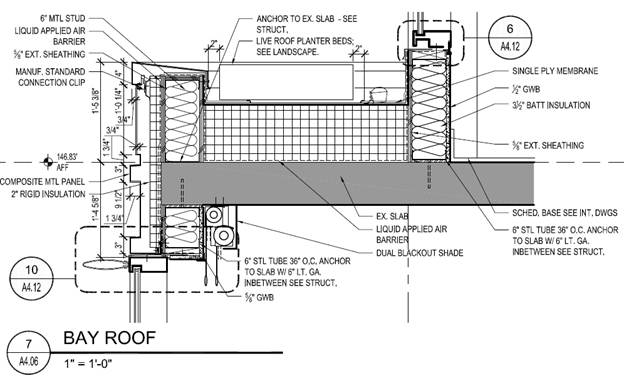
Part 2
The renovation of the Concordia Hotel requires the demolition of the entire MEP and Architectural systemsand lastly some of the Structural systems and the extensive amount of Architectural systems. The structure is located in the heart of Washington D.C., the specific address has been purposely withheld due to owner’s requests. The project is located near Dupont Circle. The Whiting-Turner Construction Company is the General Contractor (GC) responsible on the renovation project of the outdated fifty plus year old structure.
Since the project is located in a very urbanized area, a detailed construction plan, sequence and schedule will be utilized for the Concordia Hotel to ensure timely project completion. The construction process will begin with the demolition of all the existing interior and exterior walls and the extensive architectural façade. This demolition will also include the removal of the stair/elevator core of the structure. Once demolition and asbestos abatement is complete, the rehabilitation of the foundation will begin. This rehabilitation will continue up and throughout the structure and consist of the construction of new beams, columns, and slabs as well as the rehabilitation of key slabs throughout the building. The construction project was planned to be handed over to the owner in December 23rd, 2012 this handover date has been pushed back extensively due to technicalities with construction.
Electrical/Lighting
The electrical system will consist of 13 transformers. The sizes of these transformers are a 3, 6, 9, 15, 30, 45, 75, 112.5, 150, 225, 300, 500 and 750 KVA transformers. There will be 28 panel boards located throughout the building faced with the task of providing power to equipment and systems located on each floor in different regions of the structure. The main utility electric will come in from the eastern side of the structure and travel into the main electrical room located in the cellar of the structure. In the main electrical room (located in the cellar) the electric will be fed into the Main switchboard (MS-1), a 4000A 208/120V-3phase 4W 100KAIC system which will distribute electric to the remainder of the building. MS-1 will then provide power to DPR-1 which will provide service to the LPR-1 and the LP-POOL for the major pool equipment. MS-1 will also service DPC-1, DPL-3, SLPC-1ELPC-1 and AHU-2 located on the roof of the structure. The electrical system will have a 15 KVA Uninterruptable Power Supply (UPS) system utilizing an Automatic Transfer Switch (ATS) and a generator located in the garage level of the structure. Turner’s renovation of the Concordia will include the installation of LED down lights in many of the corridors as well as many other LED fixtures throughout the building.
Mechanical
The mechanical system will consist of two Air Handling Units (AHU); responsible for conditioning and circulating the air for the entire building and one Makeup Air Unit (MAU) for providing supply air for the building. AHU-01 will be a 100 % outside air packaged energy recovery AHU which will be electric heat. In figure 18 the AHU-01 is highlighted in blue, it will be located in the mechanical room cellar and it will service the ground level. The detail and location of AHU-01 is shown in figure 19. AHU-02 will also be a 100 % outside air packaged energy recovery AHU; however, it will be gas heat. AHU-02 will be located on the rooftop and will be responsible for servicing the guestrooms its location is shown highlighted in yellow in figure 22 and the mechanical section is shown highlighted in yellow in figure 23 as well. MAU-1 will be a 100% outside air MAU which will be indirect gas-fired and it will be located in the cellar level in the same location as AHU-01 shown highlighted in red in figure 18. The MAU mechanical section is shown in figure 19 with the MAU highlighted in red. I have attached product information for the AHU-01, AHU-02 and the MAU-1 below in figures 20, 21 & 24. The building will have nine (9) fans for the many areas requiring ventilation which will be five (5) supplies, one (1) exhaust, one (1) return and two (2) exhaust/returns. As I stated in my Building Statistics there will be new Variable Refrigerant Volume (VRV) systems installed into the structure as well as eleven (11) VRV air cooled condenser outdoor units located on every floor, and three (3) air cooled split system located in the fire control room the IT/telecom room and the elevator control room. Lastly, there will be two (2) electric unit heaters and one (1) relief hood.
Structural
The Concordia Hotel was constructed in 1965, the structure consists of Cast-In-Place (CIP), non-post-tensioned slabs. The renovation of the Concordia includes the extensive rehabilitation of the structural systems throughout the structure. The rehabilitation of the structure includes improvements to the foundation, columns, beams and slabs. These rehabilitation techniques were applied to the structure in order to compensate for layout changes and the installation of two new stairwells. This rehabilitation of the structure begins in the cellar level and consists of the installation of 78 Micro Piles with 42 inch thick mat slabs. The elevation to the bottom of exterior footings is a minimum of 2’-6” below finished exterior grade in most areas and in others is defined on the structural drawings. The cellar level Slab-On-Grade (SOG) is typically 5-8”. The rehabilitation continues above on floors 1-10 and includes slab strengthening techniques which include the installation of several new column types, beam types and the application of Carbon Fiber Reinforcement Panels (CFRP) to both the bottom and top of the slabs. The beam schedules and CFRP layouts are included below. These beams support the roof which also supports the high roof which houses a mechanical room and several crucial mechanical systems.
First Floor Beam Schedule (New Construction)
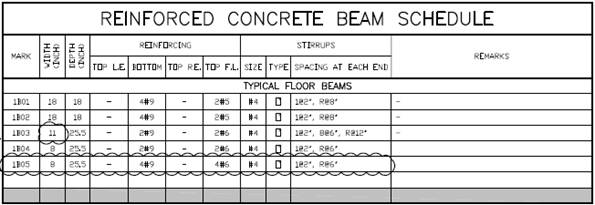
Even & Odd Floor (Floors 2, 3, 4, 5, 6, 7, 8, 9, 10) Beam Schedule (New Construction)
High Roof Beam Schedule (New Construction)
The installation of the CFRP panels will typically be installed to the even floors above and below the slab to increase the structural integrity of the slabs.
Fire Suppression
The fire suppression system that will be used is a combination of a wet-pipe system and a dry-pipe system in areas where the freeze thaw cycle is likely to occur. A Peerless model T41 jockey pump combined with a Peerless Model 6AEF10 Horizontal Splite Case Fire Pump. The pump and jockey pump will distribute water to the sprinkler system and maintain water pressure throughout the building. The loading dock will have a dry pendant fire sprinkler system (based on winter freezing conditions) connected to the wet-pipe system located in the heated ceiling space. Details are provided below of typical pendant style sprinkler heads. All work shall be installed in accordance with NFPA 13, 14, 20, and all other applicable codes.
Transportation
The existing elevator core had only two elevators, one freight elevator and one passenger elevator. The existing core was removed to make room for the new elevator core which would have three elevators. The Concordia Hotel has two passenger elevators and one freight elevator.
The existing stair well/elevator core has been demolished and two new stairwells have been installed. This installation required the strengthening of key slabs through the construction of several beams, columns and CFRP. The new construction of the two stairwells will be located on either side of the structure.
Telecommunications
Due to the structure being an extended stay type hotel there will be security rooms and security systems installed to limit the building access only to approved hotel guests. The project will also have key audio visual/information technology equipment to provide guests with the capabilities that they desire.
|