University of Cincinnati Athletic Center -
Cincinnati, Ohio
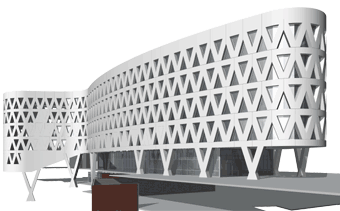
Rendering courtesy of Bernard Tschumi
Architects
• |
Building Name: University of Cincinnati Athletic Center
(now named the Richard E. Lindner Center) |
• |
Location and Site: University of Cincinnati “Varsity
Village”, Cincinnati, Ohio |
• |
Occupant : University of Cincinnati Athletic Department |
• |
Function: Multi-use, including offices, a ticket center,
meeting space, computer labs, locker rooms, an auditorium,
and gymnasium facilities |
• |
Number of Stories: 8 total (5 above grade, 3 below) |
• |
Size: 220,000 ft2 total (150,000 ft2 above, 70,000 ft2
below) |
• |
Primary
Project Team:
|
Design Architect
– Bernard Tschumi Architects |
|
|
Local Architect
– Glaserworks, Inc. |
|
|
Design
Engineer – Arup, New York |
|
|
Structural
Engineer of Record – THP Limited, Inc. |
|
|
MEP
Engineer of Record – Heapy Engineering, LLC |
|
|
CM Advisor –
Turner Construction |
• |
Construction Dates: May 2003 – December 2005 (expected) |
• |
Estimated Cost: $50.7 million |
• |
Project Delivery Method: Design-Bid-Build, State of Ohio
– low bidder |
• |
Architecture
The overall architectural design of the UC Athletic Center
is characterized by its unique exterior façade. The façade
consists of a triangulated “exo-skeleton” of
concrete-covered steel. This skeleton, sometimes referred to
as a “diagrid”, forms a visually dominant shell around the
building. The heaviness of this exterior system is offset by
its light color and by the fact is appears to be lifted off
the ground by a series of v-shaped columns. Also unique to
the building is its curved shape. There are no corners in
plan, creating a rather unusual kidney or “link-pin” shape.
The interior space of the building itself is divided by a
5-story atrium running down the middle of its main section.
To each side are offices, meeting rooms, and administrative
areas. Below ground is a more conventional rectangular
footprint, with mainly sports facilities and locker rooms.
Horizontal movement through the building is kept simple by
its compact design, however vertical movement is facilitated
by a set of elevators and a grand staircase in the atrium. |
|
|
• |
Major National Model
Codes
The building code used for this project is the 1998 Ohio
Basic Building Code. Other major codes and standards are:
Structural - ACI 301, AISC LRFD Design Specs; Mechanical –
ASHRAE 90; Electrical – NEC 2002. All disciplines also
reference the University of Cincinnati Design Guidelines and
Standards Manual. |
|
|
• |
Zoning and Historical
The building sits on an extremely tight site between the
Nippert Football Stadium and Shoemaker Center. The footprint
bends to accommodate the existing facilities, however, part
of the Shoemaker Center will be demolished to eventually
connect to the UC Athletic Center below grade. The Athletic
Center is the centerpiece in a multi-facility construction
plan dubbed the “Varsity Village”. It has been designed to
become the main architectural and social link between all
current and planned athletic facilities. |
|
|
• |
Building Envelope
The building envelope is primarily composed of the
triangular diagrid mentioned above. This system is used for
the exterior walls of the four uppermost levels. The system
skeleton consists of steel W-sections with concrete casings.
Most of the triangles contain offset glazings, however some
have concrete fills to create a smooth, continuous surface.
Below grade is a typical concrete retaining wall system and
slab on grade. The roof is a 4” normal weight topping on
steel deck and framing. |
• |
Electrical
Power for the building is taken from a 12.5 kV campus loop.
Medium voltage switchgear in a redundant double-ended unit
substation transforms the utility tap down to 480/277V.
A 480V switchboard located in an adjacent room distributes
power to each floor's electrical closet vertically via cable
feeders in conduit. Voltage is then transformed down
to service 208/120V panelboards, where it is fed to branch
circuits. Sufficient spare capacity is provided for
future loads. Typical 20A grounded power receptacles
are placed in each room. Isolated circuits are
provided for computer equipment outlets to reduce
detrimental harmonic effects. An 800 kW diesel
generator supplies four hours of autonomous backup. |
|
|
• |
Lighting
The majority of luminaires are high-efficiency fluorescent
modular ceiling recessed fixtures, predominant in the office
and non-public areas. Compact fluorescent with rapid
start electronic ballasts are also used. Local
switches and occupancy sensors provide their control.
In more specialized spaces, such as kitchens and
multi-purpose rooms, tungsten accents lights and track
lighting combine with time programs and scene set dimmers to
allow detailed control. In the atrium, linear
fluorescent lamps with louvers respond to daylight levels in
the atrium through the use of an array of light level
sensors. The exterior diagrid facade is floodlit in an
upward direction by luminaires with changeable optics.
Emergency lighting is provided as specified by code. |
|
|
• |
Mechanical
The building is fully air conditioned and heated. The
mechanical system is served by low velocity double wall air
handling units in two equipment rooms. Chilled water
for cooling is supplied by a University of Cincinnati
central chilled water plant. The 45 degree water is
metered upon entrance to the building. Two secondary,
variable speed pumps sized for 100% of the 720 ton cooling
load circulate the water. The building heating taps
into the University's campus steam system. Two
parallel pressure reducing valves reduce the loop's high
pressure steam to low pressure steam. The steam is
also converted to hot water by two straight-tube heat
exchangers, operating independently or together.
Perimeter fin tube radiation and VAV boxes with hot water
reheat condition each individual space. Zone carbon
dioxide sensors connected to the Building Management System
control indoor air quality. |
|
|
• |
Structural
The foundation consists of concrete spread footings and
drilled piers socketed into sound, interbedded shale and
limestone. Retaining walls
1'-6" thick provide some lateral stability and are braced by
the basement slabs. A section of the foundation is
connected to the existing below-grade facilities of the
adjacent Shoemaker Center. The interior superstructure
is a composite metal wide-flange beam system, supporting
composite one-way slabs on metal deck. Most
connections are designed for shear only, with a few
cantilevers supporting the atrium walkways as exceptions.
Loads are transferred down to the substructure through
spliced columns. The exterior superstructure is a
triangulated diagrid, mentioned above, which provides both
gravity and lateral bracing. The diagrid acts as a
rigid, continuous "deep beam". It is supported by a
series of V columns, moment-connected to the diagrid and
foundation. Internal lateral cross bracing also
resists the wind and seismic loads. |
• |
Fire
Protection
Active fire protection occurs through the fire alarm and
sprinkler systems. The fire alarm system is fully
addressable and networked throughout the building.
Remote annunciation panels are provided.
Horns, strobe lights, smoke detectors, pull stations, and
door release are integrated into the system. The
entire building is served by an automatic combined sprinkler
and standpipe system, connected to the 12" campus water
main. It is a wet system, with quick-response fusible
link or frangible bulb sprinkler heads. Areas where
freezing occurs are protected by an automatic dry type
system. Pressure-reducing valves regulate smoke
buildup pressures on each sprinkler connection.
Standpipes are equipped with 2.5" hose valves, but no hoses.
In the case of fire during power loss, 1250 gpm fire and
jockey pumps are connected to the emergency power supply. |
|
|
• |
Transportation
Horizontal transportation is facilitated by the dual-sided
nature of the building. Most of the building is split
into two sections by a main corridor running North/South.
This corridor includes the main atrium and elevator lobby.
The atrium is bridged at each level from East to West to
allow easier movement from one side to the other.
Outside the building, circulation is maintained by walkways
under the perimeter overhangs. Vertical transportation
is provided by 6 stair cases and 3 elevators. Only one
of the stairs, the one included in the atrium, spans
the full height of the building. Another provides
access to a nearby parking garage only. The rest
service the above-grade floor levels and provide fire-rated
stairwell enclosures for emergency egress. The three
elevators are situated in the heart of the building and
their adjoining lobby opens to the atrium corridor at each
level. |
|
|
• |
Telecommunications
Sophisticated Audio/Visual distribution network throughout
the facility. This includes cable, ethernet (2 systems
- data and video), cat 5 telephone, and wireless. Wall
mounted combination voice/data outlet boxes provide
telephone and ethernet access in the vast
majority of offices, conference rooms, meeting spaces, etc.
Additional Audio/Visual equipment will be installed in the
multi-purpose auditorium room. |
|
|
• |
Special
Systems
Although sustainable design is not by definition a "system",
the guiding principles behind the Leadership in Energy &
Environmental Design (LEED) impact all of the above systems.
For example, the structural system will incorporate local
and regional materials and the mechanical equipment has been
designed to optimize building energy performance while
offering a better health environment for occupants.
The design of the entire building aims to achieve LEED
certification from the U.S. Green Building Council. |
This page was last updated on
Wednesday April 21, 2004.
This page was created by Brian
Genduso and is hosted by the AE
Department. |