BIG EXECUTER MPSG
Big Executer is the shop floor controller. It takes
messages from simulation and directs the messages to corresponding equipment
level controller. After the task is executed by the equipment level
controller, BIG-E collects the verification messages from the equipment
level controller and sends a conformation message to the simulation
telling that the task is executed successfully. The accessibility graph
for BIG-E is the most complex of all the controller graphs since it
has to cover the whole shop floor equipment.
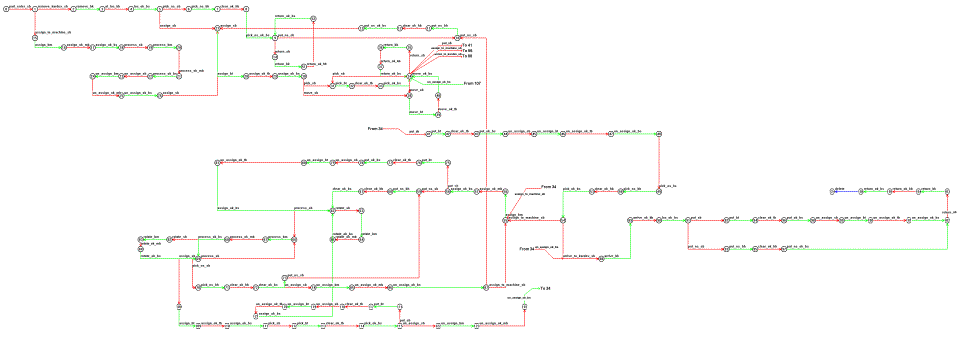
Click on image for larger
view
The accessibility graph begins with the entrance of a
part into the system. Trough out all the accessibility graphs, the red
arcs represent in-arc transition, blue arcs represent tasks and green
arcs represent out-arc transitions. When a part is introduced to BIG-E,
it can either begin its progress in the graph from the KARDEX AS/RS
or HAAS SL20 with bar feeder. SL20 with bar feeder is assumed to be
the entrance machine since it has a bar feeder that is capable of feeding
the raw material (bar stock). If the part enters the system from the
KARDEX AS/RS, it is assumed that the part is in the form of pre-cut
bar stock stored in the KARDEX AS/RS.
If the part enters from KARDEX, it is assigned to MT/MH
(material handler and transporter) and picked up by MT/MH from KARDEX.
If it enters from SL20 with bar feeder, then it is first processed in
the SL20 and then assigned to MT/MH and picked up by MT/MH. After MT/MH
picks the part, it can transport the part to any workstation in the
system. The move loop at node 34 is for this purpose. Node 34 is a junction
point since the part is transported to different workstations at this
node. The return loop at node 34 is for KARDEX AS/RS, which returns
the tray in KARDEX.
If the part goes into workstation 4, which has a manual
material handler operator then the part is put into the buffer inside
this workstation. Once MT/MH looses the possession of a part that part
is unassigned from MT/MH. Assign and un_assign messages are for the
purpose of telling simulation model that the specific resource is seized
by a part or is idle. After the part is put into the buffer and it is
unassigned from MT/MH (node 48), it is picked up by the material handler
operator inside workstation 4. At this time, the handler operator can
place the part in three different machines in the workstation. These
machines are HAAS SL20, VF-OE and VF-3. Although there are three machines,
there exist only one route in the graph for the material processor.
This is because of the similarity of the material processor controllers.
These three machines have the same accessibility graphs therefore the
messaging is the same. The only thing that changes is the parameter
that holds the machine name. BIG-E sends the messages only to the controller
of the machine identified by the parameter. The value of the parameter
(which is actually the route of the part inside the workstation) is
read by the simulation model from the manufacturing database. Generally,
this logic is embedded all over the BIG-E accessibility graph. The accessibility
graph is generic so that it can handle more than one resource, which
belongs to the same equipment class in the manufacturing system. This
means that, if three more HAAS SL20 machines are added into workstation
4, there is no need to change anything in the accessibility graph of
the shop floor executer. This property of the accessibility graph makes
it ready for certain changes in the manufacturing system configuration.
Whenever a part is done in the system, it is brought
to KARDEX AS/RS by MT/MH and placed into the tray for the finished parts.
After MT/MH puts the finished part inside the KARDEX, the tray is returned
and the part is disposed from the shop level controller (BIG-E).