ARENA
Simulation
Table of Contents
Introduction
Implementation
Experiment frame
Model frame
Animation
Introduction
The ARENA
graphics simulation software is a complete and flexible modeling environment
combined with an easy-to-use graphical user interface. It is designed
for building computer models that accurately represent real world applications.
ARENA integrates all simulation-related functions like animation, input
data analysis, model verification, and output analysis--into a single
simulation modeling environment. The real-time package is capable of
sending messages to third-party controller software for real-time control
of automated systems. In real-time mode the simulation clock operates
just like a real-time clock.
In this
project, ARENA RT (real-time) is used to control the whole system of
eight equipment level controllers through a master controller called
Big-executer (Big-E). Basically, the simulation model reads the order
entries and the corresponding master production schedule from the manufacturing
database and sends the required messages to Big-E. After sending the
message, the simulation model waits for the verification message from
Big-E telling that the command has been executed properly and the system
is ready for the next message. Consequently, ARENA simulation sends
a sequence of messages throughout the processing of a shop order, which
direct the part inside the physical system. Upon the completion of an
order, the simulation model updates the order entry table in the manufacturing
database verifying that the order has been completed and ready for shipment.
Top
Implementation
The simulation
model is the main decision maker in the system. It checks for the orders
in the manufacturing database and sends the necessary messages to shop
floor controller (Big-E) for execution. The connection between the simulation
model and the database is established through the use of a custom dynamic
link library (MSUSERC.DLL) that has been previously developed. This
file is the link between the database and the simulation model. Before
running the simulation model, the dynamic link library has be defined
in the ARENA run setup.
When the
simulation model is ran, it first connects to the router software in
order to communicate the shop floor controller, Big-E. The communication
is established over the Local Area Network. After connecting to the
router software, the model asks for the name of the manufacturing database.
As explained in the database section, the manufacturing database should
be previously defined in the ODBC Data Sources as a system data source.
After the database file is selected the simulation model starts running.
In the animation view, the busy resources can be tracked to understand
the part routings. The animation view also includes the counters for
number of parts present in the system and the number of parts that have
been completed from the current work order.
Top
Experiment
Frame
Experiment
frame includes the declarations of the ARENA simulation model components
such as attributes, variables, queues, resources etc. All the messages
sent to the execution system are defined in the experiment frame.
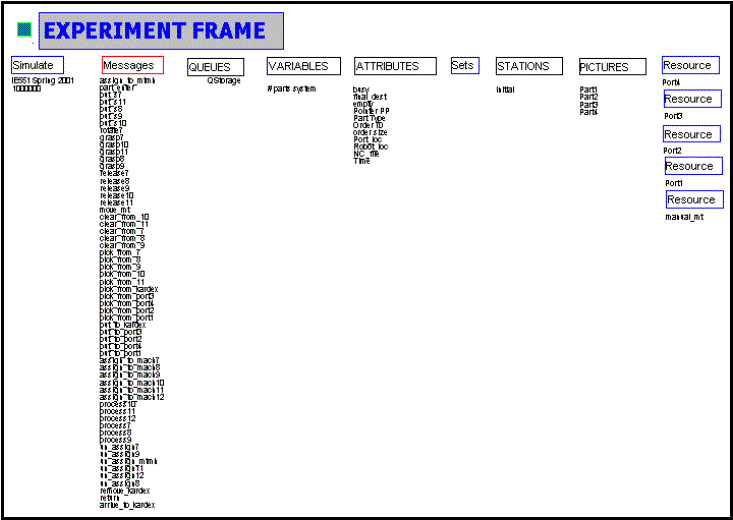
The messages
are defined with nicknames in the simulation model since the message
structure is long. Each message has its own parameters. The parameters
are actually the attributes in the simulation model and the values of
the parameters are read from the manufacturing database and assigned
to the attributes by the DLL file. There is a single attribute, sm_Execute,
which tells ARENA if the system is in execution mode or not. In the
execution mode, ARENA actually sends the messages to the router software.
In the emulation mode, as opposed to the execution mode, ARENA does
not send the messages and just emulates the run. If sm_Execute has a
value other than zero, then the system will be in execution mode.
Top
Model
Frame
Model frame
is composed of seven distinct modules of SIMAN code. Each of these modules
contains the logic for a specific part of the automated manufacturing
system in the FAME Lab. These modules are as follows:
1. Check
for new order in the manufacturing database
2. Get information
on part type and make the decision on part release
3. Departure
from Workstation 2 (remove part from KARDEX AS/RS)
4. Workstation
3 HAAS HS1RP with pallet exchanger
5. Workstation
4 (HAAS SL20, VF-OE, VF-3 and human material handler)
6. Workstation
1 (HAAS SL20 with bar-feeder)
7. Return
finished product to Workstation 2 (arrive into KARDEX AS/RS) and dispose
the entity
Module
1. New order checking

This module
creates a dummy entity every 30 seconds to initiate an event for user
coded DLL file to check for a new order entry in the manufacturing database.
Event 1 calls a function in the DLL file to check for a new order entry
in the manufacturing database and if there is one reads the order size
and assigns it to an internal attribute in the simulation model.
Module
2. Get information on part type and make the decision on part release
See
Module 2
This module
creates the entities that represent the work order in the manufacturing
system. The scan block controls the release of the entities into the
system by checking the status of the HAAS SL20 with bar feeder and the
material transfer operator, since these two members of the system are
required to be idle for the part to progress in the system at the beginning.
Since the system does not have a logic for deadlock detection and complex
resource scheduling, for now the system can be utilized only as a flow
shop if more than one part is permitted inside the system. This means
that a work order cannot have different part types those require different
routings in the system simultaneously. When a work order is decided
to be released into the system, the initiating message of part_enter
is sent to the Big-E which creates a new object in the execution system
representing the part in the manufacturing system. The new part has
two possible routings, it can either start as a bar in the bar feeder
or it can start as a raw material stored in the KARDEX AS/RS.
Module
3. Departure from Workstation 2 (remove part from KARDEX AS/RS)
See
Module 3
After the
part enters the system from module2 it comes to this module if it is
a raw part stored in the KARDEX AS/RS. The part is first assigned to
the material transfer operator and then removed from the KARDEX by the
operator. The next step is to transfer the part to its next machine
in the routing. The route block direct the transfer operator to the
next workstation in the routing of the part by checking the internal
attribute port_loc. The event 3 blocks in all of the modules reads a
line from the routing summary of the part
Module
4. Workstation 3 HAAS HS1RP with pallet exchanger
See
Module 4
This module
governs the processing of a part in HAAS HS1RP with pallet exchanger.
The material transfer operator first places the part in the machine
and then the tombstone is rotated to orient the part for machining operation.
After the part is processed, the tombstone is rotated and the part is
unloaded from the machine. In case of another process on this machine
the choose block redirects the entity to the event block after which
the process message is sent to the system.
Module
5. Workstation 4 (HAAS SL20, VF-OE, VF-3 and human material handler)
See
Module 5
Third module
is the largest of the seven. The reason is it includes three machines
and the material handler inside workstation four. When a part enters
workstation four, it will be put into the buffer inside workstation
four. Then the material handler inside the workstation picks the part
from the buffer and places in the machine that is the next in the routing
of that specific part. The routing is being read from the database by
the event block as in the previous modules. Once the part is in one
the machines, the part program is loaded and the part is being processed.
When the processing is done, the part is removed from that machine and
placed either in the buffer or placed in another machine depending on
its routing. When the part is placed in the buffer, the material transfer
operator picks up the part and transfers to the next station in the
routing.
Module
6. Workstation 1 (HAAS SL20 with bar-feeder)
See
Module 6
Module six
is very similar to module four. The machine is HAAS SL20 with bar feeder
instead of HAAS HS1RP. In this module there is no rotation messages
and no reprocessing since this lathe is not used for more than one operation.
Module
7. Return finished product to Workstation 2 (arrive into KARDEX AS/RS)
and dispose the entity
See
Module 7
When the
part is completed, the material transfer operator transfers it back
to the KARDEX AS/RS. After the part is placed in KARDEX, the number
of parts in the system is decreased by one, and the number of completed
parts is increased by one. The event block at the end triggers the function
in the DLL file that updates the manufacturing database. Every time
a part is completed from an ongoing order, the number of unfinished
parts in the database is decreased by one by the DLL file. When all
the parts are completed the work order entry is erased from the database.
At the very end the entity is disposed from the simulation.
Top
Animation
ARENA has
the capability of animating the simulation model. When simulation is
used for control of the manufacturing systems, animation provides a
small-scale visual representation of the on-going activities in the
manufacturing system. Therefore, it is very useful for monitoring of
the physical system and real-time statistical analysis.
The system
in this project is animated in ARENA. The status of the resources can
be seen in the animation during the run and the parts can be tracked
looking at the resources. The animation can be improved by assigning
images to parts that will provide the ease in following the parts during
a production run.
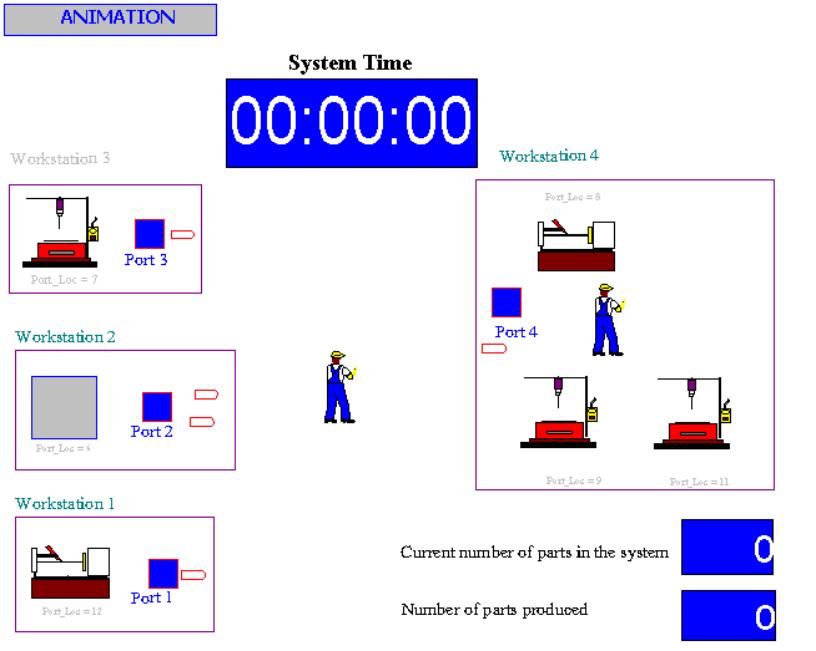
The human
figures represents the operators who are responsible for handling and
transferring the parts in the system. The human operator in the middle
have permission for transferring the among the workstations whereas
the material handler inside workstation four is only permitted to handle
the parts inside workstation four. Therefore, the operator in the middle
has more flexibility than the one in the workstation and he is called
MTMH denoting material transporter and handler.
The clock
at the top operates as a real-time clock during the control run and
the counters at the bottom-right shows the number of parts present in
the system and the number of parts completed from the current work order.
Each port denotes the entry and exit location for that workstation.
When any of the resources (either the handlers or the machines) becomes
busy, a busy indicator appears on that resource.