Process Planning
A Preliminary List of Topics
(i) Engineering Representation
1.1 Engineering Design
1.2 Part Design Drafting
1.2.1 Multiview Drawing
1.2.2 Partial Views
1.2.3 Conventional Dimensioning and Tolerancing
1.3 Geometric Tolerancing
1.3.1 Basic Geometric Characteristics
1.3.2 Symbolic Modifiers
1.3.2.1 Maximum Material Condition (MMC)
1.3.2.2 Least Material Condition (LMC)
1.3.2.3 Regardless of Feature Size (RFS)
1.3.2.4 Comparison of Symbolic Modifiers
1.3.3 Datum Referencing
1.3.3.1 Immobilization of Part
1.3.3.2 Datum Features
1.3.3.3 Specification of Datum Features in Order of Preference
1.3.3.4 Establishing Datum Surfaces
1.3.4 Positional Tolerances
1.3.5 Form Tolerances
1.3.6 Orientation Tolerances
1.3.7 Profile Control
1.3.8 Runout
1.4 Design Interpretation
1.4.1 Tolerance Stacking
1.4.2 Examples
1.5 Conclusions
(ii) Process Capability
2.1 Overview
2.2 Process Boundaries
2.3 Cutting Parameters
2.4 Basic Machining Calculations
2.5 Tool Life
2.6 Machining Force and Power Requirements
2.7 Introduction to Process Optimization
2.7.1 Cost and Time Models
2.7.1.1 Single-Pass Model
2.7.1.2 Multi-Pass Model
2.8 Summary
(iii) Process Planning
3.1 Introduction
3.2 Types of Process Planning
3.3 Manual Process Planning
3.3.1 Experience-based Planning
3.3.1.1 Machinist's Handbook
3.4 Variant Process Planning
3.4.1 Preparatory Stage
3.4.2 Production Stage
3.4.3 Example of Variant Process Planning
3.4.3.1 Family Formation
3.4.3.2 Database Structure
3.4.3.3 Search Procedures
3.4.3.4 Plan Editing
3.4.3.5 Parameter Selection
3.4.4 Advantages and Disadvantages of Variant Process Planning
3.5 Generative Process Planning
3.5.1 Introduction
3.5.2 Forward and Backward Planning
3.5.3 Input Format
3.5.3.1 Software Code
3.5.3.2 Description Language
3.5.4 Decision Logic
3.5.5 Advantages and Disadvantages of Generative Process Planning
3.6 The Use of Group Technology Codes in Process Planning
3.6.1 Basic Concepts in Group Technology
3.6.2 Implementing Group Technology Coding Schemes
3.6.3 Group Technology in Process Planning
3.7 Computer-Aided Process Planning
3.7.1 Implementation Considerations
3.7.2 A Survey of Process Planning Systems
3.7.3 A Generalized CAPP Model
3.7.3.1 Components of a CAPP System
3.7.3.2 Process Plan Knowledge Representation
3.7.3.3 Inference Mechanism
3.8 Summary
3.9 References
(iv) Process Plan Representations
4.1 Introduction
4.2 Alternate Process Plans
4.2.1 Need for Alternate Process Plans
4.3 Decision Tables and Decision Trees
4.3.1 Decision Tables
4.3.2 Decision Trees
4.4 Graphical Representation of Process Plans
4.4.1 AND/OR Graphs
4.4.1.1 Interpreting AND/OR Graphs Using Software
4.4.1.2 Implementation in Shop Floor Control
4.5 Considering Material Handling and Transport in Process Plans
4.6 Summary
4.7 References
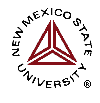
|