

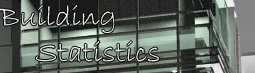

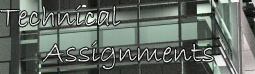






|
|
Building Statistics
General Data
- Building Name: George Washington University School of
Business and Public Management
- Location and Site: 2201 G Street, NW Washington, DC
20052
- Building Occupant Name: George Washington University
- Size: 170,000 Sf
- Number of Stories Above Grade: 6
- Total Levels: 8
- Project Team:
- Dates of Construction: January 2004 -December 2005
- Cost Information: $34,000,000
- Project Delivery: Design - Bid - Build
Building System Information
Architecture:
The New School of Business and Public Management was
designed as a single, monumental, distinctive facility that would
reflect the open nature of exchanging ideas. The building is being
erected as an addition to the existing building on the George Washington
campus near downtown Washington DC. Upon completion, the new building
will provide students and faculty with classrooms, interaction areas,
faculty and staff offices, and will become a facility which allows
the school to interact with alumni, business, professional, and governmental
organizations. The south west corner of the building displays a pillar
of glass which houses study lounges for students. These lounges will
be lit during the night time to create a welcoming beacon of light.
The first floor has a majority of student spaces, including an auditorium,
a café, a student lounge, a market lab, a classroom and a larger
lobby area that is open to the floor above. Individual areas are provided
for facets such as graduate students, faculty, and the dean’s
office. There is a terrace on the 6th floor for the dean’s office
It is a mixed use building, including post secondary
education classrooms and offices, low hazard storage and parking and
assembly. The hazard storage is for a fuel oil storage room located
in the lower level of the garage.
Building Envelope:
The addition will be post-tensioned concrete slab with
concrete column construction and pre-cast concrete panel exterior
enclosure. The two levels of underground parking garage will share
the existing ramp system. Egress means are meant to function separately
from Funger Hall, except on the underground garage levels.
The majority of the exterior is clad in pre-cast concrete. To add
character to the building, the portions of the P1 level above grade
are clad in stone, which is also used for all exterior benches which
are integrated into the exterior of the building. Above the main entrance
is a glass and steel canopy. There are coated aluminum composite panels
along the east side, behind which are the mechanical rooms. The roof
is topped above the 6th floor and has a composite aluminum cornice
running around the top of the building. On the roof is the penthouse,
which is clad in EIFS and houses some of the electrical systems.
- Zoning: Site zone classification: R-5-D
- Proposed use: Educational
-
Height limit was 90’, with the total lot being
a size of the lot being 92,577 sf while 75% of that was allowed
for occupancy purposes. Any structure on the roof could only be
18.6’ and could only take up .37 of the floor space.
Major National Codes:
- Building – BOCA National Building Code / 1996
- Plumbing – ICC International Plumbing Code / 1995
- Mechanical – ICC International Mechanical Code / 1996
- Energy – CABO Model Energey Code / 1995
- Electrical – National Electrical Code / 1996
Construction:
The construction on the new addition is type 1B or
equivalently modified type 2A. Demolition was done on portions of
the existing school so that the new building could be tied in. There
was no existing building on the proposed site for the addition, so
building demolition was not necessary. Construction is expected to
be completed in December 2005.
Electrical:
A new power distribution system was provided for the
new addition to the Business School with the main feed for the building
coming from existing Funger Hall. The main feed is run into three
15KV switchgears, which in turn distribute the power into the rest
of the building. The switchgears step the power down to a 3 phase
120/208 V power for receptacles, a 3 phase 480/277 V system for lighting
and motor loads, and a 3 phase 120/208 V system for receptacle loads
that are on an isolated ground system. The switchgears are on the
lowest floor, P2 and feed the rest of the building from there. All
conduits are run vertically through the electrical rooms by way of
a cut out in each floor of the electrical room.
The motor control center is on the roof in the penthouse.
There is a 250 kw 480/277V generator in the penthouse as well. The
generator provides power for the building, 480/277 V power for lighting
which is stepped down to 208/120 V for the motor systems in the building.
Electrical Power Systems Description (Provided by
Il Kim at Smith Group Inc.)
A. General
1. The electrical power for the new addition will
be fed from the existing spare 15 KV switch in the existing switchgear
room on the P2 level of Funger Hall to the new electrical room
in the new addition. This electrical room will be a main source
of the electrical power distribution which will include a 15 KV
load interrupter switch, 2500 KVA, 13.2 KV- 480/277 volt, 3 phase,
4 wire, dry type transformer, a 4000 amp, 480/277 volt, 3 phase,
4 wire distribution switchboard, all distribution panels, one
300 KVA, 480-208/120 volt, 3 phase, 4 wire K-13 rated transformer
for the computer loads, one 300 KVA, 480-208/120 volt, 3 phase,
4 wire transformer for the general purpose loads, and a 45 KVA
480-208/120 volt, 3 phase, 4 wire transformer for the emergency
loads.
B. Emergency Power Distribution
1. There will be a 200 KW, 480/277 volt, 3 phase,
4 wire diesel generators on the penthouse in weather proof enclosure
for the emergency loads including a fire pump, an elevator, emergency
lights, the stair pressurization fans and the life safety loads.
C. Lighting Systems
1. The interior lighting system in the new addition
will consist of fluorescent fixtures with parabolic louvers in
most areas, compact fluorescent recessed down lights and decorative
incandescent or halogen lights in the lobbies and conference rooms.
The fluorescent lights will be equipped with the energy saving
T-8 lamps and electronic ballast, All light switches will be ivory
with off-white cover plates and rated for 120/277 volt, 2-pole,
quiet type.
2. Motion sensors (occupancy sensors) will be utilized to control
lighting in private office, workstation task lights.
3. The emergency and exit lights will be provided along the paths
of egress in accordance with NFPA 101. The exit lights will be
provided with LED lamps.
D. Receptacles
1. All non-isolated ground receptacles will be ivory
colored with stainless steel cover plates. The receptacles will
be NEMA 5-20R, rated for 125 volt, 2-pole, ground type in most
areas. The isolated ground receptacles will be orange colored,
NEMA 5-20R, rated for 125 volt, 2-pole, grounding type, orange
in color.
E. Fire Alarm System
1. The fire alarm system for the new addition will
be extended from existing fire alarm system that was upgraded
three years ago. The fire alarm system will be shall be solid
state, multiplex, addressable fire alarm system that consists
of graphic annunciation panel at the new entrance lobby, manual
pull stations, audio/visual devices for the high rise building,
flow switches, tamper switches, smoke and heat detectors.
2. The fire alarm extender panels will be provided in the electrical
closet if necessary.
3. All smoke and heat detector bases will be universal mounting
base.
4. The fire alarm system will be connected between the building
security system and the campus central security console.
5. The fire alarm system can be monitored from a desktop computer
and a printer can provide output of every fire alarm activities.
6. The smoke and heat detectors for the elevator system will be
interfaced with the elevator controllers for the elevator recall
and shut down requirements.
Lighting:
The lighting for the interior building is all fluorescent
lights. Fluorescent lights were chosen for their efficiency and longer
life than most other lamps. The classrooms were primarily lit with
direct indirect lights with accenting light in the classrooms for
the white boards in the front of the room. Hallways are lit with 2x2
troffers, and most of the main lobby areas use the 2x2’s as
well. Ceiling washes are used to create ambient light in the lobbies
so that all the light is not direct.
The student lounges in the corner of the building are
unique. Because they are surrounded with glass, the lighting was important
in this space as to create a light tower at night. Compact fluorescent
lights were used to make the space functional for students wishing
to study in the lounge. Fluorescent wall washers are used on the two
walls which can be seen from outside. This is to create a bright back
ground and a glowing surface to be seen at night.
The exterior of the building and the parking garage
were lit with Metal Halides. Most garages usually have high pressure
sodium lights installed, but metal halide was used here to provide
a whiter light. The exterior is lit simply. Spot lights light the
walk ways around the building, and provide washes and spots on the
more important parts of the building.
The majority of the rooms in the building take advantage
of dimming capabilities. Each classroom and learning area has preset
dimming settings so the light levels can easily be changed on a whim.
This system is set up to include occupancy sensors that will also
determine if the lights should be shut off or not. This saves energy
by automatically shutting off lights when they are left on.
Mechanical:
Two garage exhausts vents are run with the elevator
and exit with the elevator shafts. Two air conditioners were placed
in the top floor with the elevator motors and exhaust to help control
the temperature level. Supply fans have been placed on the P2 and
P1 level to provide air throughout the building. Condensing units
are supplied throughout the building.
The primary cooling source for the building is chilled
water provided by the refrigeration plant located in the penthouse,
which will be distributed from cooling coils of the various air-handing
units. Cooling towers are provided to cool the condenser by vaporization.
AHU preheat coils supply heated hot water. The unit heaters and perimeter
finned tube convector pumps are located in the adjacent Funger Hall
along with a steam to hot water heat exchanger. There are two central
station air handling unit provided per floor in the mechanical equipment
rooms, and the air handling units provide different climate controls
for the varying spaces throughout the building.
Structural:
The addition will be post-tensioned concerete slab
with concrete column construction and pre-cast concrete panel exterior
enclosure. Live loads were calculated according to BOCA code 1996
with the roof life load being 65 lbs/sq ft for raid load. Footing
for the structure are minimum 2.5’ below grade. Post tension
design is designated on the drawing with final force and tendon profile
for each column beam or girder is provided on the drawing. Adequate
lateral bracing was required, particularly in the pit walls in the
basement during construction.
Fire Protection:
To provide safety to occupants of the building the
system is set to visually and audibly indicate an alarm, transmit
the alarm signal to remote station equipment, sound and display local
fire alarm notification appliances, transmit signals to elevator control
panels, transmit signals to release door hold open devices and electric
locks at egress doors. Water flow switches are also provided with
double check valve assembly and tamper proof switches. The building
is also protected by a wet pipe sprinkler fire suppression system
and a dry pipe sprinkler fire suppression system.
Plumbing:
In the lower basement, a sewage ejector and storm sump
pump are provided to help with water loads. The loads are regulated
with a high low domestic hot water manifold station with domestic
water pressure regulating valves with mutlitple thermostatic mixing
valves to pipe water of varying pressure and with inlet stop checking
valves to help regulate the temperature on the outlet.
Telecommunications:
The business school is set up with a variety of telecommunication
systems. The Ethernet and voice wires are run separately from the
other conduit, having been provided with their own cable trays in
accordance to the wishes of GWU. All class rooms are provided with
Ethernet access, with the majority of the rooms having the Ethernet
wires core-drilled into the furniture and run through it. All classrooms
are also provided with junction boxes for Professors to use along
with TV outlets and speakers to better present various multimedia.
All offices are provided with Ethernet and phone access as well.
Transportation:
There are four elevators that access all the floors
of the building, and their motors and other accessories are located
on the penthouse in the roof, with elevator 4 being classified for
freight use. One elevator provides access from the two parking garage
levels to the first floor elevator banks. The elevators runs on 480
volt 3 phase system with an automatic transfer switch for switching
to emergency power upon the loss of power. This must be able to signal
the elevator and let it know the normal power was interrupted and
contacts that let the elevator know when power is being switched to
emergency and back from emergency. Operate at 75 horsepower. Two enclosed
stairs are located on either side of the building, these elevators
stretch from the basement to the 6th floor with one accessing the
penthouse. There is also an open stairway in the main lobby connecting
the first and second floor.
Special Systems:
Security systems are run through emergency power. The
stair wells are equipped with electric door locks. The main entrances,
including the garage entrances and the stair well doors, are equipped
with door contacts. Cameras on closed circuit television circuit are
provided through the building. Also, panic buttons and red and blue
light emergency lights are provided in case the need should arise
for the building to be evacuated. Keypads and glassbreak detectors
have also bee provided to allow for an extra degree of safety. There
are also occupancy sensors in the rooms to turn on lights if someone
should enter.
User
Note:
Note: While great efforts have been taken to provide accurate and
complete information on the pages of CPEP, please be aware that the
information contained herewith is considered a work-in-progress for
this thesis project. Modifications and changes related to the original
building designs and construction methodologies for this senior thesis
project are solely the interpretation of Brad Hartman. Changes and
discrepancies in no way imply that the original design contained errors
or was flawed. Differing assumptions, code references, requirements,
and methodologies have been incorporated into this thesis project;
therefore, investigation results may vary from the original design.
|
|