Welcome to Paul Parfitt's AE Senior Thesis e-Portfolio
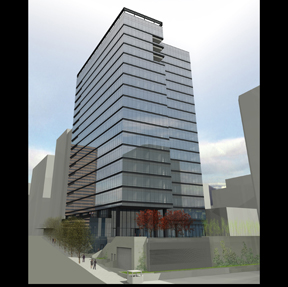
Building Statistics
Building Name: Tower 333
Location and site: Bellevue, Washington. 108th ave & 4th streetBuilding occupant name: N/A
Occupancy: Office space
Size: 400,000 sq. ft.
Number of Stories: 18
Primary project team:
Owner: Hines Development & Washington Capital Management
General contractor: LCL
Structural & civil engineers: Magnusson Klemencic
Mechanical engineers: ME engineering
Architect: LMN Architects
Dates of construction: Completion date end of 2007
Building Code: IBC 2003
Zoning: Commercial
Historical requirements of building or zone:Designed to implement a preexisting foundation and concrete core from an earlier abandoned construction project.
Building envelope: highly transparent glass curtain wall and built up roofing
DETAILED BUILDING STATISTICS
Architecture:
Designed to allow the maximum amount of daylight penetration possible while giving breathtaking views of Lake Washington and the Olympics, Tower 333 uses highly transparent windows with a full 10 foot height. Column free, open plan floors enable tenants free range of interior layout. In addition to this, Tower 333 also has a 1/2 acre landscaped plaza located on the ground floor which all add to Tower 333's LEED rating.
Structure:
Tower 333 is a steel framed structure for all 18 levels above grade. The above grade floor system consists of steel beams and girders which support 3 inches of concrete on a 2-1/2" composite metal deck. The 8 levels of below grade parking are post-tensioned concrete slabs and cast in place concrete columns. The lateral system is designed to be a dual-based concrete shear wall core in conjunction with steel moment frames about the perimeter. Tower 333's foundation utilizes an existing foundation and core which was previously abandoned at Parking Level 5 due to financial issues.
Mechanical:
Typical floor air distribution shall consist of floor-by-floor air handlers serving conventional overhead systems with series fan-powered terminal units, primary air ducts, secondary air ducts and perimeter slot diffusers.Outdoor air will be introduced through louvers at each level with the intake plenum integrated with the structural beam system.The floor terminal equipment shall be series type fan powered terminal units (FPTU) with energy efficient GE ECM fan motors and double wall construction with internal acoustical attenuation as required to maintain an NC 40 or lower in the occupied tenant space. Maximum fan CFM for FPTU’s shall be 1750 CFM for interior and perimeter zone. All perimeter fan powered terminal units, and all units on the top floor, will include electric heating coils on the discharge of the FPTU.
Perimeter slot type diffusers with down-blow center sections and integral returns will be used for overhead heating and cooling. Minimum air supply volume to interior zones shall be 0.8 CFM per square foot. An 8” high zone directly above the ceiling will be provided for tenant flexibility. No MEP services will be permitted to run in this zone, only drop through it where necessary. This zone will provide total tenant flexibility for light fixture placement, tenant cable trays for data, telephone, and communications wiring, etc.. System shall consist of (1) floor-by-floor VAV air handling system per floor. Each AHU shall supply low temperature air to overhead ductwork serving series-type fan powered VAV boxes at the perimeter. Primary air temperature is 45°F, and mixed space supply air is 51°F.
Electrical:
The new office building will be served by Puget Sound Energy (PSE) with 15kV circuits that will terminate into a 15kV transformer vault located in the parking garage level. The Contractor shall provide 6” conduits from a PSE switch cabinet vault to the transformer vault to facilitate the installation of PSE’s 15kV cabling. Emergency power system shall provide pad mounted, diesel generator(s) sized per drawings complete with double wall skid fuel tank, control panel, batteries, etc. Fuel capacity to be sufficient for 6 hours of full load run time (maximum of 480). The generator set(s) will feed all the emergency and standby loads required by code and the life safety systems. Exhaust muffler and unit mounted cooling system to be supplied with the generator set(s).
Lighting:
All interior areas of the building will be provided with a lighting system to maintain illumination levels as shown or as required by applicable codes utilizing commercial quality fixtures as specified hereafter. Lighting system will be complete with panel boards, feeders, branch circuits, and controls all as specified elsewhere. Circuiting will typically be 277 volts for HID and fluorescent lighting and 120 volt for incandescent and quartz lighting. All fluorescent light fixtures will incorporate electronic energy efficient ballasts and T8 lamps.50% of all metal halide fixtures shall have a quartz restrike for emergency egress lighting. 20% of all open office fluorescent lighting shall be fed from an emergency (diesel generator) source. Lighting controls are to provide a complete lighting control system for the building. Lighting control shall be a networked system of relay panels that are controlled by the building management system (BMS).The lighting control system shall be low voltage and its software an object oriented, Windows based system.