|

The Helena
New York, NY
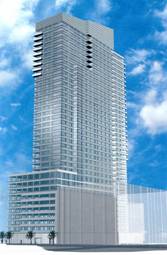
General Project Data:
Building Name:
Location:
- 601 W. 57 th Street, Manhattan, New York City, New York
Building Occupant:
- Each apartment is occupied privately by individuals or families
Occupancy Type:
- Residential Apartment Building
Size:
- Approximately 600,000 square feet
Number of Floors:
- The building is composed of 38 stories above grade and 40 stories overall
Project Team:
- Owner: The Helena Associates, LLC -- www.durst.org
- Owner's Representative: Rose Associates, Inc. -- www.rosenyc.com
- Architect: Fox & Fowle Architects, P.C. -- www.foxfowle.com
- Lobby Architect: B Five Studio -- www.bfivestudio.com
- Apartment Consultants: Harman Jablin Architects -- www.hjarchitects.net
- Structural Engineer: Severud Associates -- www.severud.com
- Construction Manager: Kreisler Borg Florman -- www.kbfgeneral.com
- MEP Consultant: Flack & Kurtz Inc. -- www.flackandkurtz.com
- Black Water Treatment Plant Consultants: Dagher Engineering -- www.dagherengineering.com
Construction Dates:
- The issue for construction was made October 3, 2003 and the building is expected to be finished in the Autumn of 2004
Cost:
- Overall building cost: $160 million
Delivery Method:
Architecture:
- The Helena will feature a 10,000 square foot green roof. The reasons for going with this design are to help lower energy costs by reducing heat gain as well as act as a rainwater retention system that will funnel water to the building’s cooling system and also help reduce water runoff into the streets. The building is a modern design of floor to ceiling glass, wrap around windows, and sleek metal panels. The windows are made up of a high-performance glass which will prevent large heat gains into the building and help create more efficient air heating and cooling. The panels, which have the capabilities of solar energy collection, will convert the solar heat to electricity which will be integrated into the electrical manufacturing plant in the building to lower overall energy costs.
Building Envelope:
- The envelope of the building is supported by a reinforced concrete frame made up of a 45% furnace slag concrete mix. Attached to the outside of the frame are floor to ceiling windows and sleek metal panels. The building is a defiance of the typical building formula of exposed concrete slabs, masonry, and through-wall air conditioning units.
Building Systems I:
Electrical System:
- The Helena is powered by one 750 KVA - 208Y/120V and one 500 KVA - 208Y/120V transformer. The transformers power two service switchboards located in the cellar. The switchboards are rated for 6000 A each and supply power to 20 metering cabinets in the east and west sides of the building on floors 3,6,9,12,15,18,21,24,27,30,33, and 36. Each cabinet serves up to 9 apartment units. The distribution panel also runs on the 208Y/120V system and is rated at 800 A. The typical apartment panel schedule runs on a 208Y/120V 1 phase system. Also included in the electrical system is a 480Y/277V system running transformers from 15 KVA to 225 KVA. This power is distributed through a 600 A rated distribution panel.
Lighting System:
- The main portion of the lighting in the building is composed of flourescent lighting. 2'x2' surface mounted parabolic troffers are used in the conference room and office areas. Among the lighting used in the rest of the building are 6" recessed compact flourescent down lights and 1'x4' surface mounted 2 lamp wraparound flourescent fixtures. The lighting on the first floor retail areas includes metal halide track lighting, recessed adjustable low voltage lighting, metal halide wall wash, and penadant mounted downlighting.
Mechanical System:
- An induced draft cooling tower highlights the mechanical system putting out 3300 GPM. Cooling is provided with one rooftop airconditioning unit supplying 3500 CFM. Heating is aided by two 1350 GPM plate and frame heat exchangers. All apartments are furnished with a console water source heat pump for heating and cooling needs. The cooling tower is hooked up to 3 water pumps which create pressure for the water flow. The cooling tower consists of two tanks located on the roof. The fuel oil storage tank is located in the sub-cellar along with two low pressure steam boilers and the heat exchangers.
Structural System:
- The foundation of the building is composed of monolithic and spread footings, some of which are anchored with 20-ton rock anchors. Retaining walls laterally braced by framed slabs and slabs-on-grade make up the sub-structure of the building. The superstructure is composed of a gravity and lateral load resisting systems. The gravity system is composed of 8" flat plate slabs and 12" one-way slabs supported by reinforced concrete columns. Shear walls which provide support in both directions creates the lateral resisting system of the building. Materials consist of reinforced concrete with a 45% furnace slag concrete mix. The exterior of the building is made up of mostly high-performance glass and solar collecting metal panels.
Building Systems II:
Fire Protection:
- Each floor is fitted with a floor control valve assembly and fire hose valve in the staircase area. The ground floor staircase houses a fire hose storage cabinet and key box. The typical floor plan is supplied water by a 2.5" diamter main pipe which branches off into smaller pipes of diameters ranging from 1" to 2" in diameter. A 6" fire service pipe enters into the building to supply water for the system. This water is sent through a manual fire pump in the cellar. This pipe is accessible from a 3"x3"x6" fire department connection at 57th street. The sprinkler flow control valve assemblies are connected to a 2" diameter sprinkler drain spill which leads to a service sink. Sprinklers are also supplied in the trash chutes, fed by 2" diameter piping. The roof contains a jockey pump and a special service fire pump which lead to a 25,000 gallon capacity water storage tank, which holds 15,000 gallons for fire reserve and 10,000 gallons for domestic building use.
Transportation:
- There are two staircases located in the building, one in the East wing and one in the West wing. Approximately in the middle of the building are 5 elevators, 1 combination elevator and 4 passenger elevators. Horizontal movement through the building is done through a corridor which is the point of access for the apartment units. Floors 12-23 have access to the roof on the north side from a door at the end of a hallway that branches off of the main corridor. Balconies are located on the 14th through 38th floors on the West side of the Northwest corner, also on the 30th through 38th floors on the East side of the Southeast corner, and finally on the 33rd through 38th floor on the North side of the building.
Telecommunications:
- The telecommunications for The Helena enters into a telephone room in the cellar floor from 11th Avenue and 57th Street. The telephone room has a telecommunications main grounding busbar, 20" long x 4" wide x 1/4" thick newton, which is connected to the stranded continuous copper telecommunications bonding backbone (TBB). This wiring is run vertically through the building using (8) - 4" diameter conduits. Starting on the second floor, each third floor houses a main grounding busbar, 10" long x 4" wide x 1/4" thick newton. A typical one bedroom apartment has a network interface device (ICC compace distribution center or equivalent) which branches out to allow for one voice only connection, one voice/data, one voice/data/cable tv, and one cable tv only connection. All connections are CAT5E.
Special Systems:
- The Helena is fitted with a roof lightning protection plan. On the roof is a copper down conductor which runs down through the building by way of 1" fiberglass conduit. The largest part of the design of this building was put into the green design. The building is capped by a 10,000 square foot green roof. The architecture incorporates solar collection panels and high performance glass. Internally, the building also has green components. A black water treatment plant housed in the cellar helps re-use the water in the building and incorporates the water caught in the green roof. Recycling is also made easy with chutes designed at each floor which can be used to dispose of recyclable materials.


|
|
|