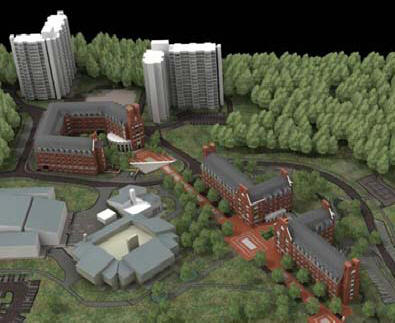
BUILDING STATISTICS
GENERAL BUILDING STATISTICS:Building Name: George Read Hall
Location: The University of Delaware Newark, DE 19716
Occupancy/Function: Residential housing complex for students
Size: Approximately 129,000 sq. ft.
Number of Stories: 5 stories above grade plus basement
Primary Project Team:
Owner: The University of Delaware
www.udel.edu
Architect: Ayers/Saint/Gross
www.asg-architects.com
General Contractor: There was no General Contractor
Construction Manager: Whiting-Turner
www.whiting-turner.com
M.E.P. and Fire Protection: Sebesta Blomberg & Associates
www.sebesta.com
Structural Engineer: Skarda & Associates
www.skardaengineers.com
Civil Engineer: Tetra Tech, Inc.
www.tetratech.com
Code Consultant: Koffel & Associates
www.koffel.com
Dates of Construction: May 2004 - August 2005
Project Cost: Building cost - $27 Million
Project Delivery Method: Design-Bid-Build
BUILDING SYSTEM INFORMATION:
Architecture:
The new George Read Hall is one of three new state of the art buildings being built on the University of Delaware's campus to replace the existing Pencader complex. The building consists of five floors of dormitory style housing with double rooms sharing a bathroom as well as single room suites. The building also features laundry rooms, fully furnished lounge spaces, kitchen space, study rooms, and building support spaces. Housing approximately 500 beds, George Read Hall is the largest of the three new residential buildings. Also included in the building are apartments for the hall directors and complex coordinator. The exterior of the "U-shaped" building combines architectural features from the surrounding buildings into a Georgian styled look. The removal of the existing buildings will make room for playing fields, tennis, basketball, and volleyball courts, and a pedestrian bridge from main campus to the new residential complex.
Building Envelope:
The exterior walls are all brick façade with many symmetrically placed windows so that each room has a window. Each window is finished with a brick jack arch above and a simulated stone sill below. The fifth floor is finished with dormers on each side of the building protruding from the gambrel style roof. The dormers are covered with metal paneling on the front and shingles on the top, matching the rest of the roof. On the north end of the building, a two story curved wall complex lounge adds an additional space for students to relax or study. The exterior of the lounge is finished with simulated stone and several rows of bricks at each floor level. Topping off the look of this complex lounge is a large storefront system with one inch insulating glass units. Exterior walls of the building consist of metal stud framing with 2" rigid insulation and an air space. The inside of the wall is finished will 5/8" gypsum board, while the outside is finished with brick or simulated stone. The roof of George Read Hall consists of asphalt shingles.
Construction:
The project began in May 2004 and took less than 15 months to complete. The building was completed on time, and students were able to move in for the fall semester 2005. The building cost approximately $27 million. The construction process was to occur while interrupting as little as possible, including activities on the campus and surrounding vegetation that was to remain. In addition, the process was designed so that none of the existing beds in the existing Pencader complex were removed until the new beds were ready for use. Deliveries to the site were scheduled so as to minimize the amount of space used for storage as well as the amount of time required for storage of materials and equipment.
Zoning and Historical:
University zoned for residential. The site is already residential housing for students. It has no historical requirements.
Major National Codes:
IBC 2000
ACI 301, ACI 318
AISC
ASME
Delaware State Fire Protection Regulations, June 2003
NFPA 101
Electrical:
George Reed Hall is powered by both 480/277V and 208/120V. The larger power supply is needed to run appliances such as dryers and stoves, while the smaller source is needed to for outlets using smaller appliances. The elevators are powered by 480 volt, 60 Hz, 3 phase, wye delta starting. Backup power is supplied by a diesel engine generator that will run at 350 kW for 17 hours.
Lighting:
As with a typical dormitory style building, many different types of lights and light fixtures were used. Typical sizes include 2'x2', 1'x4', 2'x4' as well as wall mounted lights providing direct lighting and direct/indirect lighting. Many different varieties of bulbs are used as well, including fluorescent and high intensity discharge. T4 and T8 fluorescent bulbs are used in double and triple tube fixtures. High-pressure sodium and metal-halide lamps are used in the HID fixtures. Emergency lighting is installed with batteries and chargers.
Mechanical:
The construction of the three new buildings in the residential complex required the installation of a new 750 ton chiller to accommodate the building's cooling needs. The air is supplied throughout the building by variable air volume units. The air is monitored by humidity sensors, air velocity sensors, and differential pressure sensors. Airflow ranges from 50-5,000 FPM in most situations. The temperature can be controlled by electric thermostats.
Structural:
The main structure of the building consists of cold formed metal stud framing and a Hambro composite floor system. The basement is constructed of 1'-4" thick concrete walls with #4 @ 12" both ways, both faces with a 5" thick concrete slab on grade with wire mesh. All floors consist of 14" deep Hambro joists with a 2-3/4" concrete slab spanning approximately 24'. Typical bearing walls consist of 16 gauge, 50 ksi metal studs. Typical basement bearing walls consist of 3-6" metal studs spaced at 12" on center. The first floor and second floor walls consist of 3-6" metal studs at 16" on center. The third floor requires 2-6" metal studs at 16" on center, and the top two floors require 1-6" metal stud at 16" on center. Each floor is also laterally braced with x-braced shear walls. The foundation of George Read Hall consists of a continuous concrete footing of varying width around the perimeter of the building and spread footings on the interior. Typical columns are HSS 6x6x5/16. The curved wall at the complex lounge is constructed of curved W12x14's. Roof framing consists of prefabricated light gauge trusses @ 2'-0".
Fire Protection:
The building is equipped with an automatic sprinkler system. The sprinkler system is both wet-pipe and dry-pipe type systems. Spray on fireproofing is always used on the beams and columns. Exit enclosures provide a two hour fire rating and occupancy separations provide a one hour fire rating. The fire protection system includes manual pull stations, audio devices, smoke detectors, heat detectors, and duct detectors.
Plumbing:
The building water supply is heated with commercial electric water heaters with a pressure rating of 150 psig. The sump pumps have a capacity of 15 gpm with 1-1/2" diameter discharge pipes.
Telecommunications:
Each room unit is equipped with phone and Ethernet jacks as well as cable hookups for television. Two telecommunications rooms are located on each floor and a main telecommunications room is located in the basement. As with most universities, access to the building will require authentication through card readers at the doors.
Transportation:
George Read Hall is equipped with two hydraulic passenger elevators running from the basement to the fifth floor. The elevators are rated at 3500 pounds and travel at 125 feet per minute. They are equipped with battery powered lowering. If the power fails, cars at a floor level will open their doors and shut down. Cars between floors will be lowered to a pre-selected floor, open their doors, and shut down.