Building Statistics
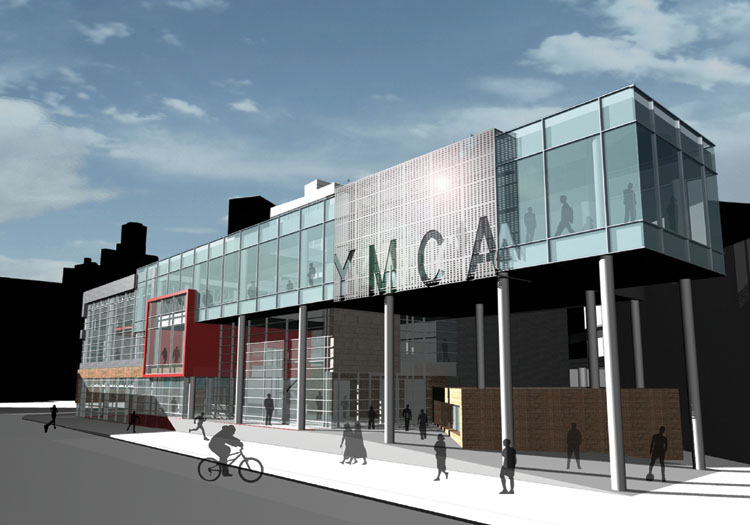
GENERAL PROJECT DATA
Building Name: The Downtown Family YMCA
Location/Site: 1401 Broadway, Detroit, Michigan
Occupancy Type: II-A, Recreational
Size: 110,000 SF
Number of Stories: 4
Dates of Construction: January 2004 - December 2005
Project Cost: $29 Million
Project Delivery Method: Construction Manager with a GMP
PRIMARY PROJECT TEAM
Owner: YMCA of Metropolitan Detroit
Construction Manager: Barton Malow Co. - Southfield, MI
Architects and Engineers: SmithGroup - Detroit, MI
Consultants:
– Theatre - American Society of Theatre Consultants
– Natatorium Pool - Water Tech, Inc.
– Site Utility Relocation - Tucker, Young, Jackson, Tull, Inc.
ARCHITECTURE
•Architecture: The new $29 million YMCA will be downtown Detroit's first new YMCA in over 90 years. Located near the heart of the city, the new Y will have much to offer. A feasibility study conducted in the early planning stages helped determine the features to best meet the community's needs. The result: beyond the fitness center, the building will include a performing arts theatre, arts and humanities center/studio, sports arena, child care/family resource center and a natatorium, with lap lanes, a whirlpool and family play areas. Its distinctive stepped shape is due to its unique and challenging site. Since the main priority for this building is high visibility of what's going on in the different facilities, a design concept was carried out to have '1/2-levels.' What this means is that certain floors in certain parts of the building are staggered. There is also going to be a fountain outside (which the owner is pursuing). There is a climbing wall in the lobby, elevated running track above the gym and a pool in the basement. The goal of the this building is to get families to come downtown who might not want to come downtown without a reason, and get them to have a great experience and want to stay and then want to come back
•Codes: The Downtown Family YMCA was designed in compliance with IBC 2000 as its primary code with Michigan Ammendments. Design loads were in accordance to ASCE 7-98. Design seismic loads are based on:
-seismic use group:1
-building category: II
-seismic importance factor: 1.0
•Zoning and Historical: This building was built in accordance to the City of Detroit Official Zoning Ordinances. Its unique location and shape of the site presented many challenges. For one thing, there is a 'people mover' track that runs right by the site so it had to be a certain distance away, and restricted the use of cranes and movement of goods. Not to mention that the same zoning laws applied in regards to the new parking structure being built right next to it and the existing buildings around it. The new Y is being erected on a former parking lot. Aside from buried rubble and some old brick foundations, excavators found little of interest when preparing the footings. A problematic leaky water main under the site was eventually repaired.
•Building Envelope: The building is composed of a decorative CMU masonry and glass facade. Instead of going with panels, a cavity wall was built. The glass panels in the lobby/atrium area have been modified so that they can tilt out. This was done to coordinate with the mechanical system installed to create constant air-flow in case of a fire. A Kawneer curtain wall system was used for the main entrance/atrium as well as the visible fitness rooms. The original roofing system was designed to be built up, but because cost cutting was a major issue with this building, a single ply roofing system was chosen instead. Besides this, Vulcraft acoustical decking was used and a multi-ply asphaltic roof memberane was applied over rigid insulation of varying thickness. An aluminum style parapet coping is used around the perimeter of the roof - at all varying elevations
ELECTRICAL
The building's main transformer is 1500kVA at 480/277V Y - 3 phase. The main breaker consists of a 2000AF/2000AT insulated case at 480V, 3HP. The secondary feeders provide 3000A of current at 480Y/277V lighting panels and (9) 208/120V receptacle panels. There is an installation of 100 linear feet of DTE duct bank. The duct bank is concrete encased and houses two 4" PVC conduits. There is also an installation of 100 linear feet of SBC duct bank. The duct bank will also be concrete encased and house two 4" PVC conduits. The emergency light ballasts are operated through batteries.
LIGHTING
There was a variety of different lighting used throughout this project. Every section of the Y (whether it's the pool, offices, lobby etc.) has different types of fixtures. Generally, flourescent lights were used in a variety of ways: pendants, suspended, strips and even in the pool. In ordeer to provide the best cost efficiency, all the lights and fixtures were ordered from the same manufacturer. The company that provided the lights is called Resource Lighting, located in Southfield, MI. This was done through Detroit Electrical Services.
MECHANICAL
Due to the building's 'half-levels' a major obstacle faced was the routing of all ductwork. The half levels caused the ductwork to climb, fall and work around structures at different parts of the building. On the rooftop, there are 5 different air handling units (AHU). There are 3 used for general supply at 820 CFH each, 1 for laundry at 450 CFH, and one for the natatorium at 1140 CFH. Natural gas boilers are used for the heating of water and there is also a central de-ionized/reverse osmosis water system. In addition to this, there is a dehumidification unit that provides 16,000 cfm. On the rooftop there are 5 seperate roof exhaust fans at 1000 cfm each.
STRUCTURAL
Since this building consists of multiple wide open spaces: natatorium, basketball court, and track, special considerations had to be taken in selecting the proper beam span for each section. W16x31 beams are used for the support of the basketball court/track area, while the actual track itself uses W12x14 beams. The office areas, which are located on one of the half-levels, used mainly W18x35 and had some W18x50 beams for the support of some mechanical equipment. The climbing wall in the main lobby/atrium used lateral bracing, and there were 3 types of trusses used in different parts of the building (mainly for the support of half levels). In terms of floor construction, 4000psi concrete is used for the slab on grade and a 4000psi lightweight slab on deck is used with shear studs at 1 per 48" and a 2" metal floor deck is used. The basement walls are designed for 55psf. There were no composite beams used in this project.
FIRE PROTECTION
Throughout this building you can find that an ADA compliant fire alarm system has been installed. A unique feature of this building is the two smoke exhaust fans for the atrium which provide 50,000 CFM. All in all, there are about 850 sprinkler heads and 640 concealed heads. There were even heads installed underneath the track to provide the basketball court with maximum coverage. The YMCA uses wet-type fire sprinkler system stand pipes. Also, there were 3 types of fireproofing used: spray-on applied, hand troweled, and intumescent hand applied coating.
TRANSPORTATION
There is one elevator in the YMCA. This elevator is hydraulic, services all floors and is being provided and installed by Schindler elevator company.
TELECOMMUNICATIONS
IP phone system is being used, it's a very capable system and adjustable for any future modifications. Commscope UTP data & voice cables were installed. They are category 5E 350Mhz. In terms of voice capability, 50 pair category voice transfer cables are used. SBC T1 connections are used for data, there are several Sisco wireless points, and the system is capable of gigabit transfer for desktop and ethernet. There is one main computer room and two remote closets. The closets were connected by 6 strand fiber optic cables.
The Capstone Project Electronic Portfolio (CPEP) is a web-based project and information center. It contains material produced for a year-long Senior Thesis class. Its purpose, in addition to providing central storage of individual assignments, is to foster communication and collaboration between student, faculty consultant, course instructors, and industry consultants. This website is dedicated to the research and analysis conducted via guidelines provided by the Department of Architectural Engineering. For an explanation of this capstone design course and its requirements click here.