welcome to j. david maino's ae senior thesis e-portfolio
Building Statistics
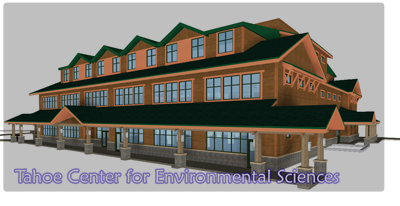
General Building Statistics:
Building Name: Tahoe Center for Environmental Sciences (TCES)
-
Location and Site: Incline Village, NV
-
Building Occupant Name: Sierra Nevada College, U.C. Davis, and the Desert Research Institute (DRI)
-
Occupancy or Function Type:
-
Primary: Research/Classroom Facilities
-
Secondary: For use as a learning/teaching tool
-
-
Size (total sq. ft.):
-
Number of Stories Above Grade: Three Stories
-
Primary Project Team:
-
Owner: Sierra Nevada College and U.C. Davis (development partner)
-
Website: http://www.sierranevada.edu
-
Website: http://www.ucdavis.edu
-
-
Architect: Lundahl and Associates
-
Electrical Engineers: Integrated Design Associates
-
Website: http://www.ideasi.com
-
-
Mechanical Engineers: Rumsey Engineers
-
Lighting Designer: David Nelson & Associates
-
-
Dates of Construction: May 2005 – November 2006
-
Cost: $24 Million (overall project cost)
-
Project Delivery Method: Design-Bid-Build
Building System Information:
Architecture:
-
Architecture (design and functional components):
-
Interior: Due to strict zoning requirements (see below) the design of the building was constricted to a square shape, which did not lend itself well to daylighting. As a result, a central atrium that filters light to other spaces is a major design focus of the building. Classes, labs, offices and conference rooms branch off of this central space. The first floor houses common spaces, as well as office space for DRI, the second floor is comprised of lab spaces, classrooms and offices for Sierra Nevada college, and the third floor houses U.C. Davis’ facilities.
-
Exterior: Fiber-cement siding panels molded painted to look like cedar wood panels adorn the exterior façade. The use of recycled materials in the siding promotes the “minimum impact” idea that is central to the TCES project. Pitched roofs help prevent snow build-up as well as provide ideal placement for photovoltaic panels and solar hot water collectors. Overall, these features lend themselves to a “cottage in the woods” type feel
-
Zoning: Tahoe Regional Planning Agency (TRPA) oversees all planning and zoning for the Tahoe Lake region. Strict height, footprint, and ecological impact restrictions are enforced by TRPA. These in turn create numerous design and planning challenges. An excerpt from the TRPA website (http://www.trpa.org) explains that “[t]he Tahoe Regional Planning Compact calls for the Regional Plan to establish a balance, or equilibrium, between the natural environment and the human-made environment.”
-
Historical Requirements: None.
-
Building Envelope/Roofing System: The building envelope is primarily a stud wall framing system utilizing thermal insulation and moisture barriers to prevent thermal losses and mold. The exterior is covered with fiber-cement siding on the upper stories, with a portion of the first story covered by a CMU veneer. Glazing on the exterior is a low-e, argon gas filled, 70% transmissive glass which reduces thermal losses through the building envelope when compared to traditional glazing systems. The roof of the building is built upon a steel wide-flange framing system. It is comprised of a mechanically attached thermoplastic membrane over 3” DensDeck Prime™ on top of rigid insulation applied to metal roof decking. Snow guards are strategically placed to prevent snow and ice from falling into paths of engress and egress.
-
Special Design Considerations: TCES is currently designed to be certified as 8 points above LEED platinum, with the building being 8 points over platinum before final commissioning. Due to the nature of the research conducted at the site, the owner wished to set an example for the community and show that new construction need not be wasteful or energy intensive as well as having as little impact as possible on the fragile ecology of the Lake Tahoe Basin. As such, it is important to the owner to retain this level of LEED certification.
Primary Engineering Systems:
-
Construction: Construction began in May of 2005 and will take approximately 18 months to complete, at which time the client will move in and begin their use of the building.
-
Electrical: The main service coming into the building is a 3Φ, 4W feeder serving a 1600A, 208Y/120V switchboard. From there, each floor is fed from several distribution panels. The basement contains one 600A, 208Y/120V distribution panel which feeds a 225A panel and numerous motor loads, including hot and chilled water pumps. The second floor also contains one 600A, 208Y/120V which feeds several panels and several fan coil units. Finally, the third floor contains another 600A distribution panel which serves several other panels and fan coil units.
Supplementing the main service is a series of (9) photovoltaic arrays with a total of (87) tile elements located on the roof. These PVs provide DC power which is converted to AC using an inverter with a built-in disconnect. Due to code restrictions, the arrays are tied into the main system via a 100A panel in the basement with an additional means of disconnect. Also supplying an additional 30kW of power is a Capstone MicroTurbine cogeneration unit which supplies 480V and is connected to the grid via a 480Y-208/120 transformer. Due to slow starting times on the cogeneration unit, a separate 50kW back-up generator is used to provide emergency power to the building. This unit is activated by means of an Automatic transfer switch located next to the switchboard in the basement.
-
Lighting: Daylighting systems played an important role of the design of TCES. Light shelves along the perimeter work spaces help block out direct sunlight, and serve to push useful daylight up toward the ceiling to provide indirect lighting for the spaces. Additionally, a solarium within the lobby of the building allows daylight to filter down into the lobby, as well as workspaces adjacent to the solarium since there are few full-height partitions joining the workspaces and the solarium within the atrium space. Reflectors within the solarium serve to push light into the space to direct it where it can be most beneficial.
Because of the level of daylighting utilized in the building, daylighting controls were implemented. Photocells are used in conjunction with occupancy sensors as well as an automatic on/off timer to determine if electric light is necessary, as well as turning off lights in rooms that are not occupied for a certain period of time. Several “zones” are defined to turn off lights incrementally rather than all on or all off.
Pendant mounted linear fluorescents and compact fluorescent wallwashers are used in many of the spaces, with the addition of dimming ballasts being used in the multipurpose room and the case study classroom. The lobby/solarium contains compact fluorescent wallwashers and metal halide track fixtures for accent lighting. Hallways lining the solarium contain 2x4 direct/indirect linear fluorescent fixtures. Wall mounted metal halide sconces adorn the exterior of the building, as well as full cutoff.
-
Mechanical: Several unique mechanical systems are housed within the building. Radiant heating and cooling ceiling panels have been implemented in many rooms to to eliminate the need for traditional HVAC equipment, and an alternate radiant hydronic heat slab in the floor has been added to supplement the ceiling panels for the same space. The radiant floor system is comprised of a cooling tower, pumps, and piping throughout the concrete slabs. Water is pumped through the floor to condition the space. Also, the cogeneration unit mentioned previously generates heated exhaust as a result of producing electricity, which can be used to heat water or steam for use in lab applications, lavatories, or in the radiant floor system. Solar hot water collectors on the roof offer an additional source of heated water for use in the various systems of the building. The basement houses a storage facility for chilled water as well as a greywater collection system to gather rain and melting snow, which can then be used for latrines. Perimeter convection ventilation is the chosen method of ventilating the spaces, shooting a stream of high velocity air into the room, which draws air in the room because of the pressure differential.
-
Structural: The main structure is a one-way, cast-in-place, reinforced concrete slab that is 8” deep in parts, and 12” deep in others due to the use of radiant heating pipes in the floors. Supporting the slab is a series of cast-in-place beams and columns. The roof structure is supported by a series of wide-flange steel beams, upon which the roof structure described earlier is built. Slab-on-grade is a 5” thick reinforced concrete slab.
-
Fire Protection: TCES contains light hazard and ordinary hazard areas protected by wet automatic sprinkler systems. Additionally, an automatic, class “B” fire alarm system with an integral security system is in place. The fire alarm system specified is an Edwards system, which utilizes Edwards detection and security devices as well as compatible Wheelock notification devices. The main Fire Alarm Control Panel (FACP) is supplemented by Remote Notification Power Supplies which act as additional battery packs to boost power and remove the problem of voltage drop in the 24V DC system. Upon activation, the fire alarm system shuts down any HVAC units serving the affected floor, closes any mechanically held fire doors and sends a signal to a UL listed call station that an alarm is in progress. The FACP and Remote Annunciators display the location of the alarm and whether the space is currently open or closed using the security system.
-
Telecommunications: Main tele/data connections are made through the Main Distribution Frame (MDF) and telephone phone server in the basement. Data jacks are provide as a standard in most spaces, with combination tele/data jacks being supplied to offices, conference rooms, multipurpose rooms and workspaces.
-
Transportation: Three stairwells serve the upper floors and provide the main means of transportation for people within the building. An elevator supplements the stairs and provides access for those who may be unable to use the stairs, as well as a means to move large pieces of furniture/equipment throughout the building more easily.
-
Special Systems: None.